Porosity in Welding: Identifying Common Issues and Implementing Finest Practices for Avoidance
Porosity in welding is a pervasive issue that frequently goes unnoticed up until it creates significant issues with the honesty of welds. This usual flaw can endanger the toughness and longevity of bonded frameworks, presenting safety and security dangers and bring about costly rework. By comprehending the origin triggers of porosity and carrying out efficient prevention methods, welders can significantly improve the quality and dependability of their welds. In this discussion, we will certainly explore the vital variables adding to porosity development, analyze its damaging impacts on weld performance, and discuss the most effective techniques that can be embraced to reduce porosity incident in welding processes.
Common Sources Of Porosity
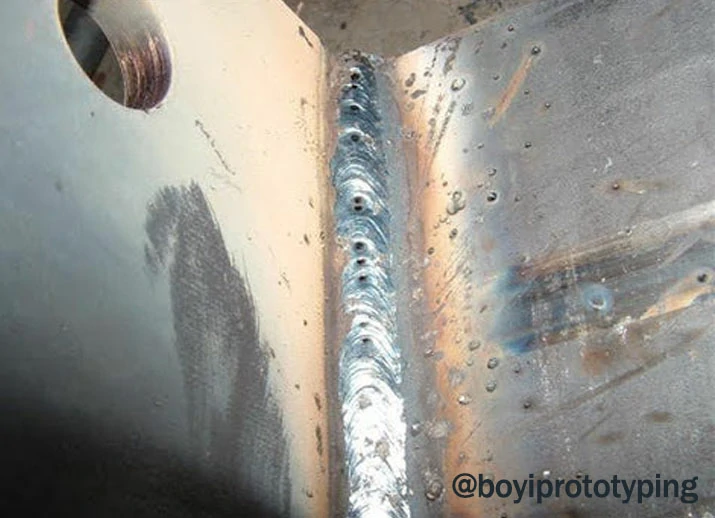
One more frequent perpetrator behind porosity is the presence of pollutants externally of the base metal, such as oil, grease, or rust. When these contaminants are not effectively gotten rid of before welding, they can evaporate and become entraped in the weld, causing flaws. Making use of dirty or wet filler products can present impurities into the weld, adding to porosity issues. To reduce these typical reasons for porosity, extensive cleaning of base metals, appropriate shielding gas selection, and adherence to ideal welding criteria are necessary techniques in attaining top notch, porosity-free welds.
Influence of Porosity on Weld Top Quality

The visibility of porosity in welding can significantly compromise the structural integrity and mechanical residential or commercial properties of bonded joints. Porosity develops voids within the weld steel, deteriorating its general stamina and load-bearing capacity. These voids serve as tension concentration points, making the weld extra at risk to splitting and failing under used tons. Additionally, porosity can reduce the weld's resistance to corrosion and various other ecological aspects, additionally decreasing its longevity and performance.
Among the primary repercussions of porosity is a decrease in the weld's ductility and toughness. Welds with high porosity degrees have a tendency to exhibit reduced effect strength and lowered capability to deform plastically prior to fracturing. This can be especially concerning in applications where the bonded components are subjected to vibrant or cyclic loading conditions. Additionally, porosity can hinder the weld's capacity to effectively transfer pressures, leading to early weld failure and possible safety and security risks in crucial frameworks.
Best Practices for Porosity Avoidance
To enhance the architectural integrity and quality of bonded joints, what particular steps can be implemented to reduce the event of porosity during the welding process? Making use of the right welding method for the specific product being bonded, such as readjusting the welding angle and weapon position, can even more prevent porosity. Regular evaluation of welds and immediate remediation of any issues identified throughout the welding process are necessary methods to protect against porosity and generate visit this site right here high-grade welds.
Significance of Appropriate Welding Techniques
Carrying out proper welding methods is extremely important in guaranteeing the structural integrity and high quality of bonded joints, building upon the foundation of efficient porosity avoidance steps. Extreme warmth can lead to increased porosity due to the entrapment of gases in the weld swimming pool. In addition, using the appropriate welding criteria, such as voltage, existing, and take a trip rate, is essential for accomplishing audio welds with marginal porosity.
Furthermore, the choice of welding process, whether it be MIG, TIG, or stick welding, ought to straighten with the details requirements of the project to guarantee ideal results. Appropriate cleansing and prep work of the base steel, along with picking the appropriate filler material, are also important elements of efficient welding strategies. By sticking to these finest methods, welders can lessen the threat of porosity development and generate high-grade, structurally audio welds.
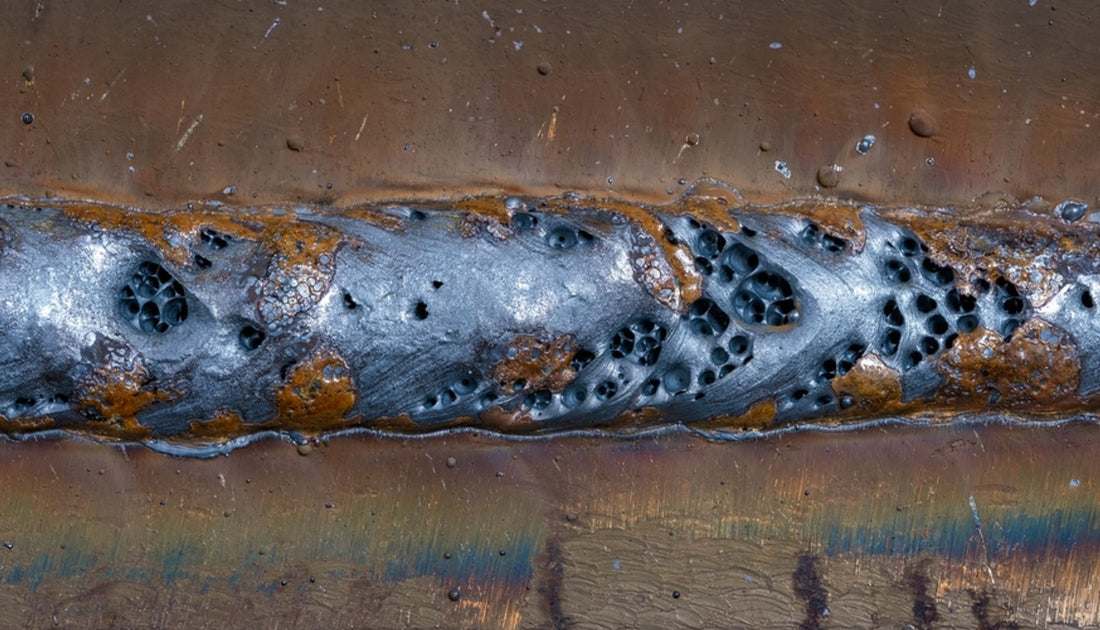
Checking and Top Quality Control Measures
Testing procedures are essential to detect and stop porosity in welding, making sure the stamina and sturdiness of the final item. Non-destructive screening approaches such as ultrasonic testing, radiographic screening, and visual evaluation are commonly utilized to recognize potential flaws like porosity.
Performing pre-weld and post-weld examinations is likewise crucial in keeping quality assurance standards. Pre-weld assessments involve validating the products, tools setups, and sanitation of the workspace her latest blog to stop contamination. Post-weld examinations, on the various other hand, analyze the last weld for any kind of problems, consisting of porosity, and verify that it fulfills specified criteria. Applying a thorough quality assurance plan that includes thorough testing treatments and evaluations is vital to minimizing porosity concerns and ensuring the general top quality of welded joints.
Final Thought
In final thought, porosity in welding can be an usual issue that impacts the high quality of welds. By hop over to these guys recognizing the usual causes of porosity and executing best methods for avoidance, such as appropriate welding techniques and testing steps, welders can guarantee top quality and trusted welds. It is necessary to focus on avoidance approaches to decrease the event of porosity and maintain the integrity of welded frameworks.
Comments on “Comprehensive Guide: What is Porosity in Welding and Exactly How to avoid It”